# 01

︎
Digital Craftsmanship
in Fashion Design
Adjunct Lecturer
( 2018. Spring - Summer )
Craftmanship, the spirit of the high-end fashion industry, has gradually disappeared under the impact of fast fashion and has seemingly only become an emotional word in copywriting or parts of a brand story.
Fortunately, in recent years such a situation has an opportunity to change because of the frequent application of digital fabrication technology. Through digital design and fabrication, the knowledge of the traditional craft can be embedded in computation. Furthermore, Martin Tamke (2013) pointed out that "A new sense of crafting emerges that does not only characterize the setup and making of digital design systems but allow designers as well to revisit local craft traditions."
Following the concept from Martin Tamke, this course tried to teach more advanced modeling and 3D printing techniques, encouraging students to think that "How can traditional craftsmanship transfer to computing field?". In response to those topics, the students chose various delicate clothing crafting such as lace, embroidery, smocking, tapestry, etc., as the theme and implement new design methods create new design proposals for those crafts.



︎ Merging different layer patterns together by programming G-code to design delicate units of the headwear. Those nylon units were re-processed by the acid dye in much time in order to make the gradient color.
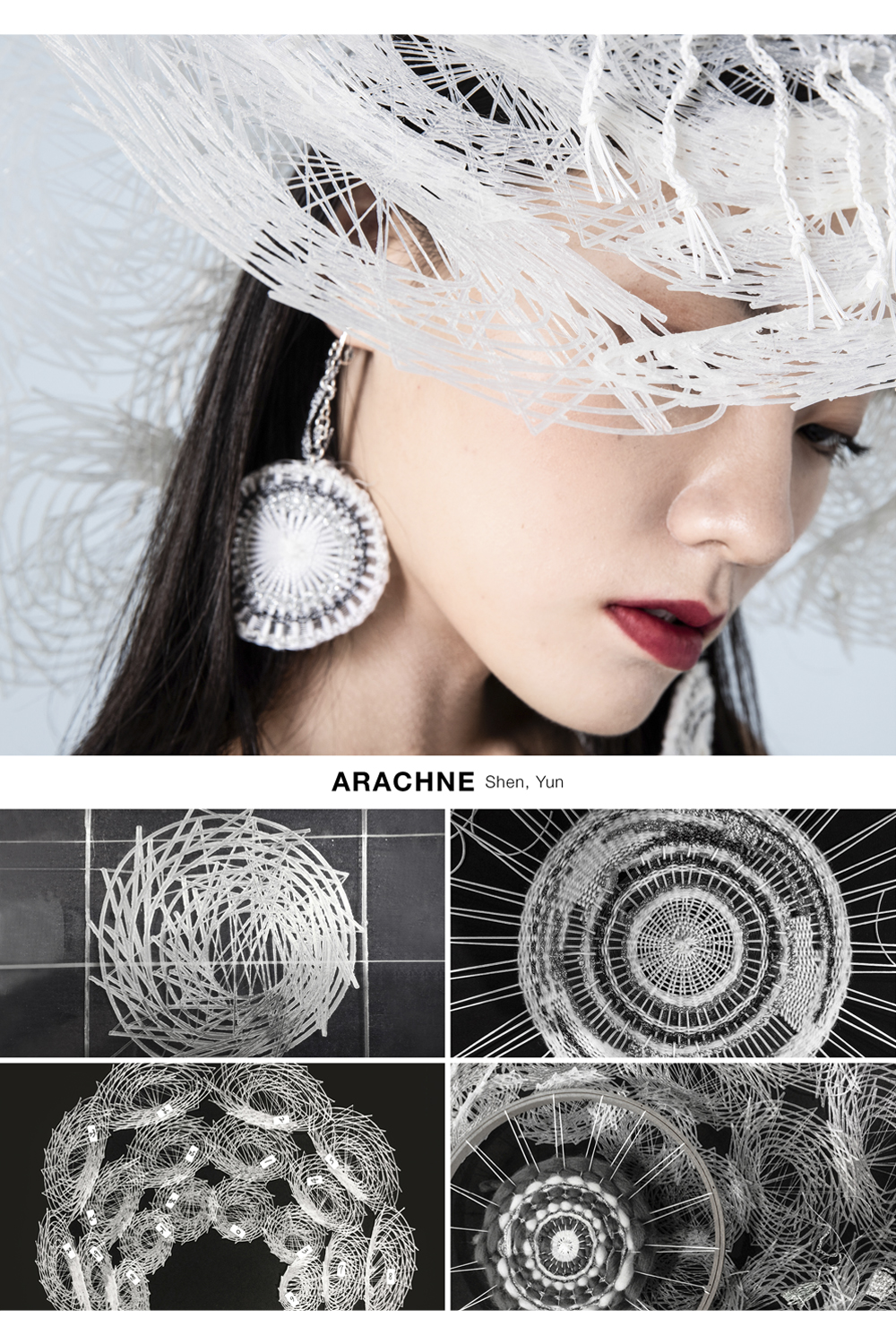
︎ Developing the new application of tapestry which structures interlace with a warp and a weft. The warp parts of this Panama hat are printed out by nylon filament and woven with various sizes, types, colors yarns.

︎ In order to reduce cut pieces, this design printed patterns on flexible fabrics to shape silhouette. According to experimental parameters, the shrink effect of fabrics was applied successfully to pocket design.
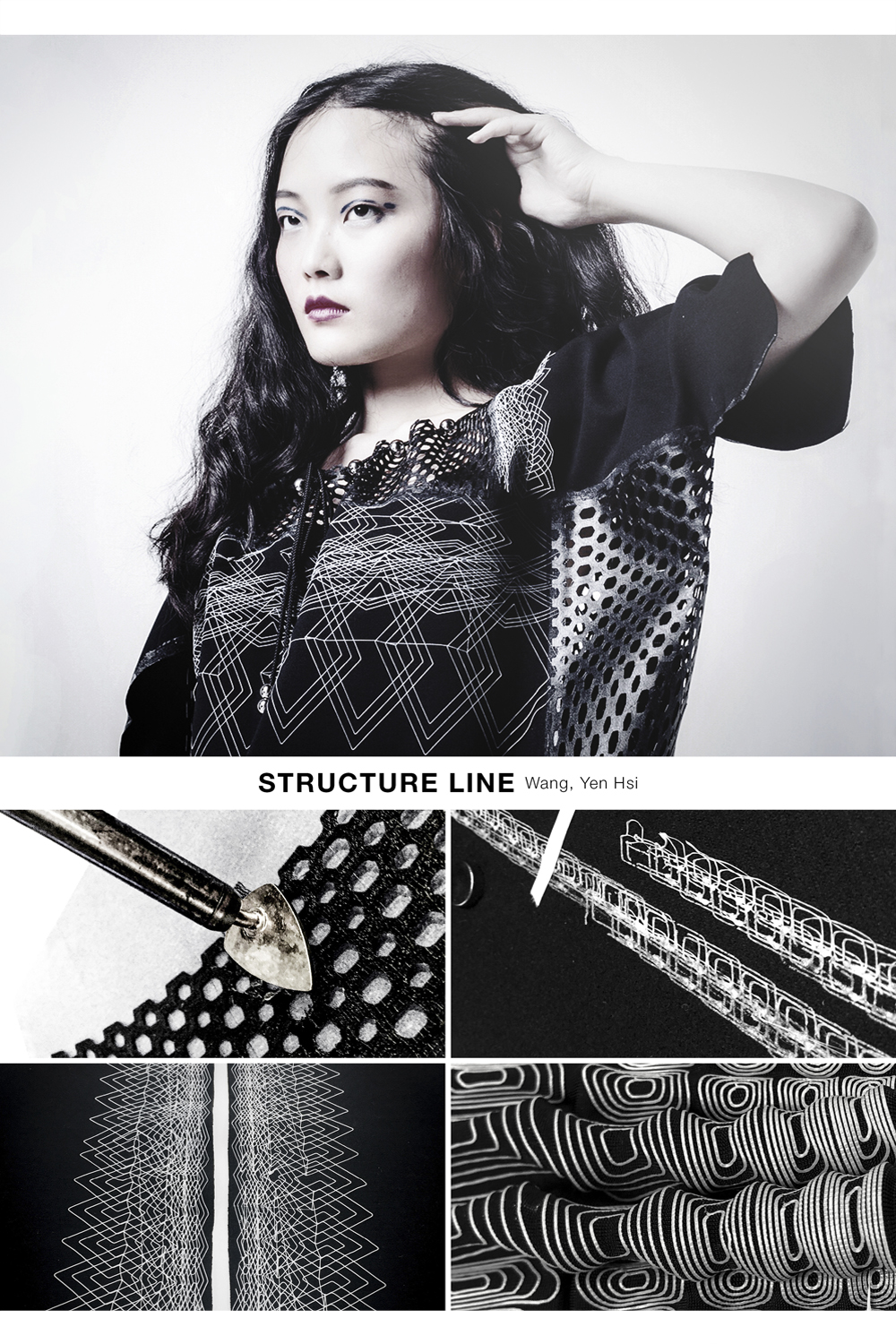
︎ Parameterizing the general structure lines and fabricating cut pieces by 3D printing /laser cutting machines. Such an approach illustrates that digital fabrication gives the chance of mass customizes for ready-to-wear industries.

︎ Generating vector lines from illustrations and then transferring into G-code for creating unique embroidery brands. The challenge of this approach is how do 3d printing brands connect with leathers firmly without sewing and gluing.
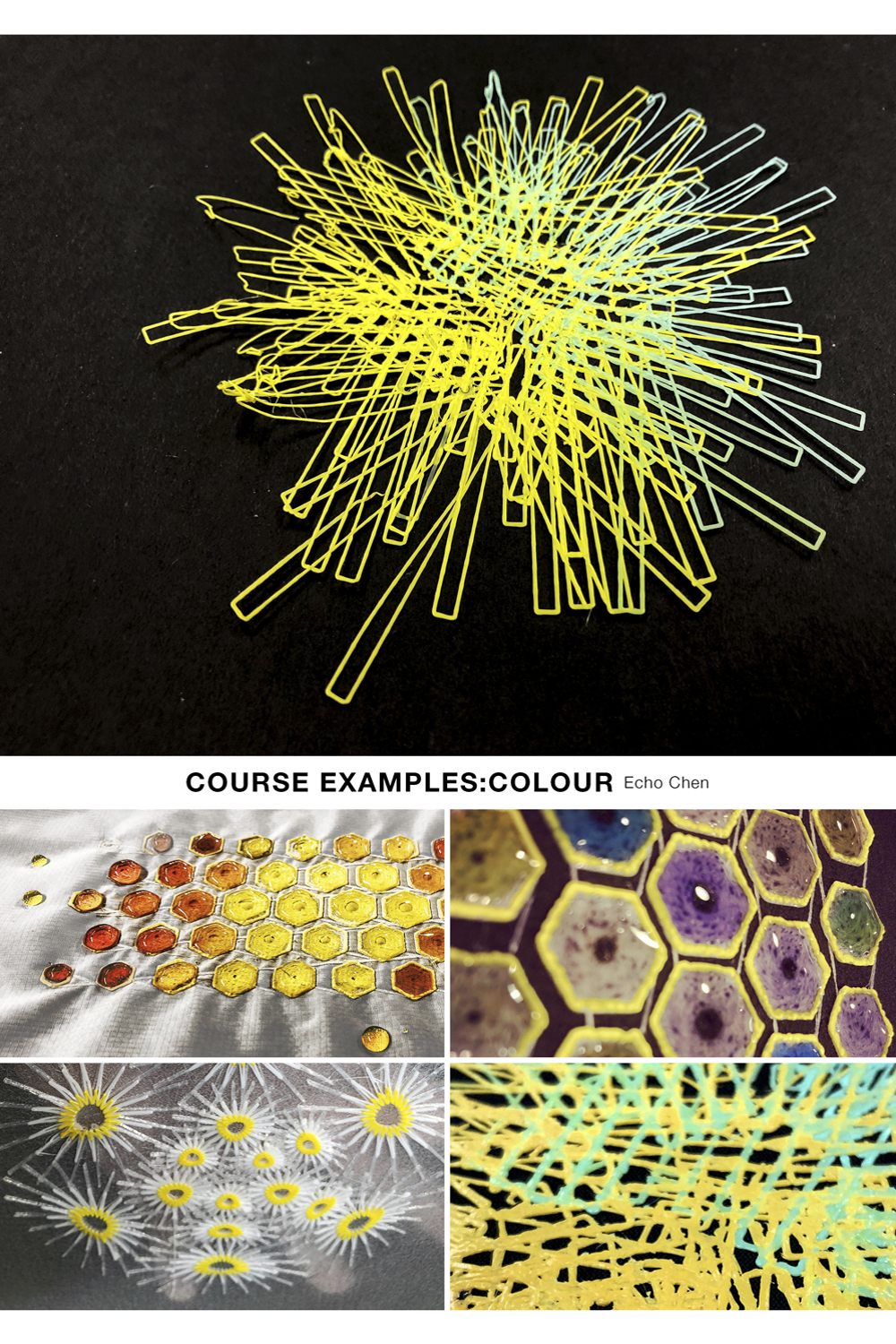
︎ Testing various 3D printing techniques / materials to develop different color effects, and printing on many types of fabrics to find the perfect one which can be attached with 3D printing parts firmly, such as Suede+Nylon.