# 01

︎
Callar Noir
Project Designer
( 2018. Summer-Fall )
Calla Noir, the decorative floor lamp at nearly 130cm tall, was designed utilizing the various control mechanisms of the 3D printing FDM process to blend the printing material and generate a surface pattern that varies through the changing of the light. Its single-layer printed lampshade expresses the coded computational movements of the machine in the pattern and finish of the printing shell. This design strategy alleviates the "problems" of FDM printed works and changes our perception of this technology from prototyping to finished product.
With the help of new performance materials from Modex 3D filaments and our fabrication partners at Linkin Factory, The project demonstrates the potential for 3D printed results as the final finished product without additional post-processing.
exhibited in 2018 Taiwan Int'l 3D Printing Show, Aug.29-Sept.1; won 2019 A' Design Award & Competition.

︎ 3D Printing Elements
the ABS plastic units printed by large delta 3D printers.
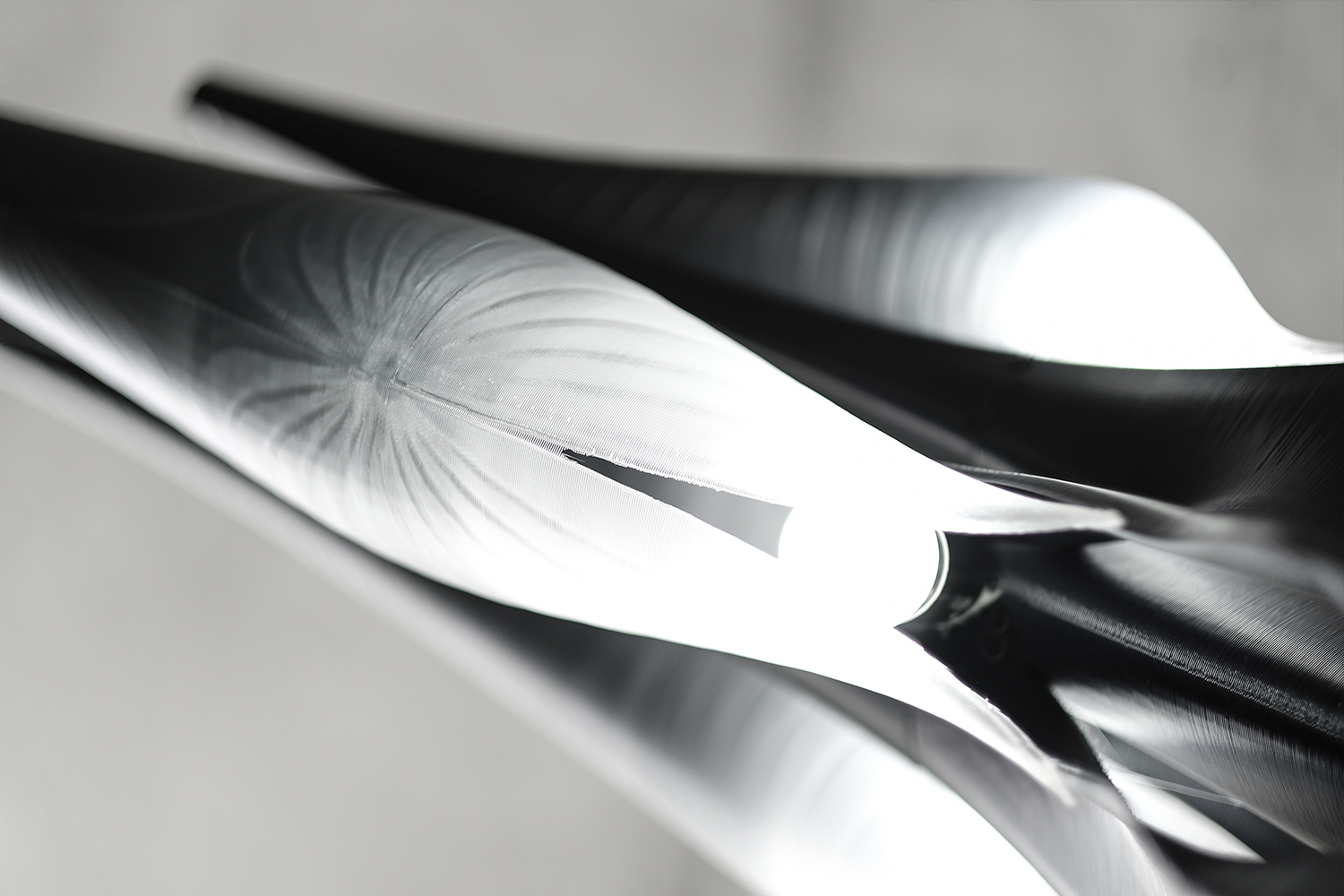
︎The details of Design
Combining with Lighting system
# 02

︎
Twirls
Project Designer
( 2018. Summer-Fall )
The motif of the design lighting piece ,Twirls , exemplifies this new translation process in FDM printing, expanding on "layer by layer" additive method to enable a higher degree of control to the finished surface texture and color transition by the designer. By focusing on the design process and the translation of computational data into material effect, this project experimented with the effects of seam parameterization, machine speed control, and gradient extrusion. The resulting single-layer printed lampshades are thus able to present elegant patterns and variations in texture and color under conventional backlighting.
Twirls not only demonstrates the unique aesthetics of the 3D printing process, but also the potential for FDM printed results to achieve the level of finish and expression found in conventionally manufactured products today. Additionally, this achievement alludes to the chance for a new generation of designers to embrace materiality through computation and manufacturing.
exhibited in 2018 Taiwan Design Expro, Aug.15-17.

Collaborating with industrial partners to building up a gradient printing system.

Translating of printing parameters into material effect through the program of G-code.

Velocity printing surface patterns on the delta printer in PING product launch.
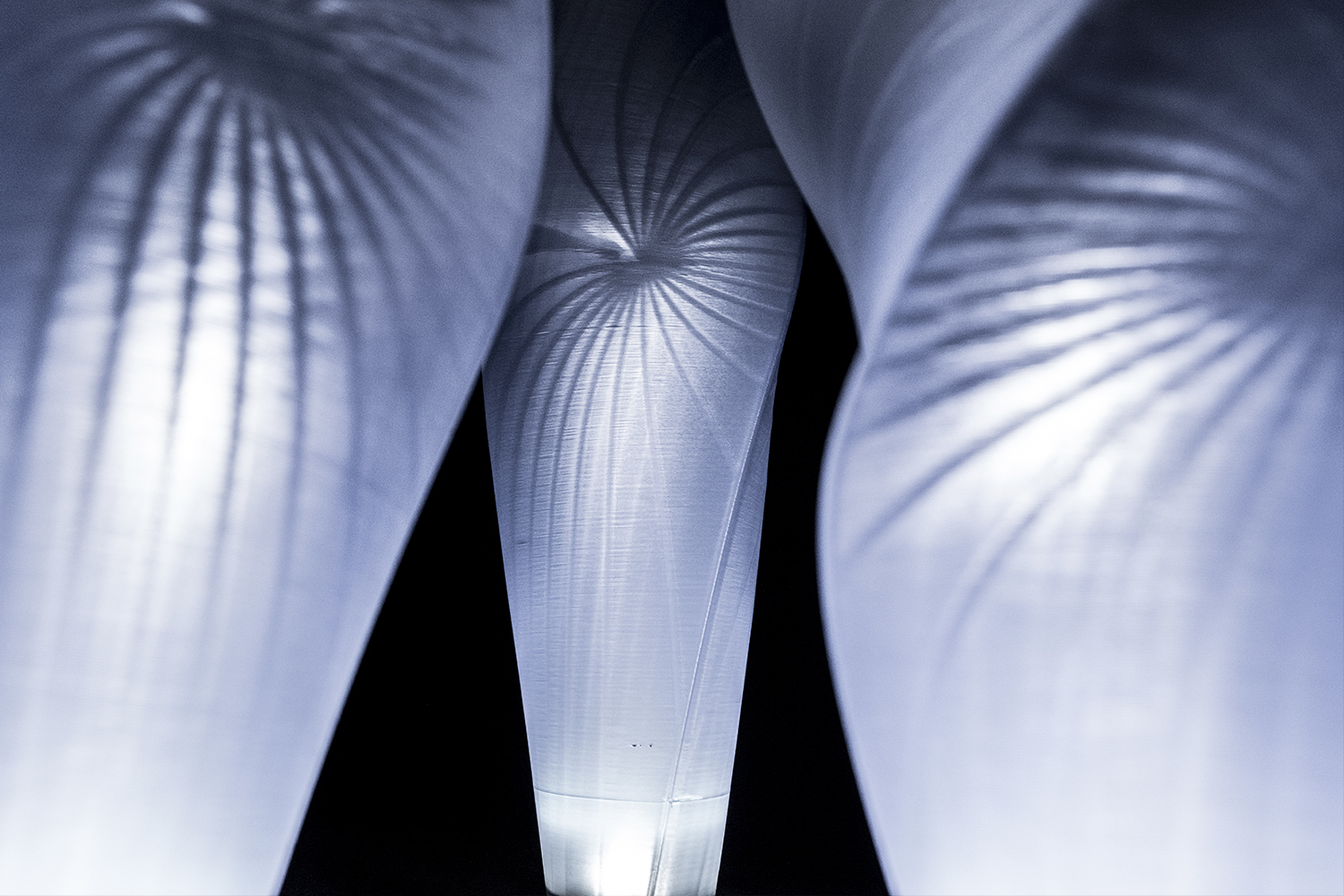
︎The Pattern on Lampshades
Testing the lighting effect of Velocity printing surface patterns.
# 03

︎
Hexapod
Interior DecorationProject Designer
( 2017. Summer-Fall )
Hexapod is a computationally defined wall lighting system derived from subdivided mesh geometry, and 3D printed demonstrating it’s direct to fabrication potential. The proposed installation is the product of the integration of both additive and subtractive manufacturing processes. While additive manufacturing and 3D printed solutions are not commonly found in final design products, the project utilizes Modex ABS 3D printing filaments, which offer excellent post-processing potential. For the bench and wall surfaces CNC milled panels made of composite layers of the Valchromat engineered colored MDF board were selected for their smooth milling finishes and colors. The addition of color layers, patterning, and milled geometry results in the emergent expression of the subtractive design method.“Hexapod ” brings the design to a new level of maturity through the rationalization of geometry and greater consideration of materials and finish.
exhibited in 2017 Taiwan Design Expro, Sept.30-Oct.15.
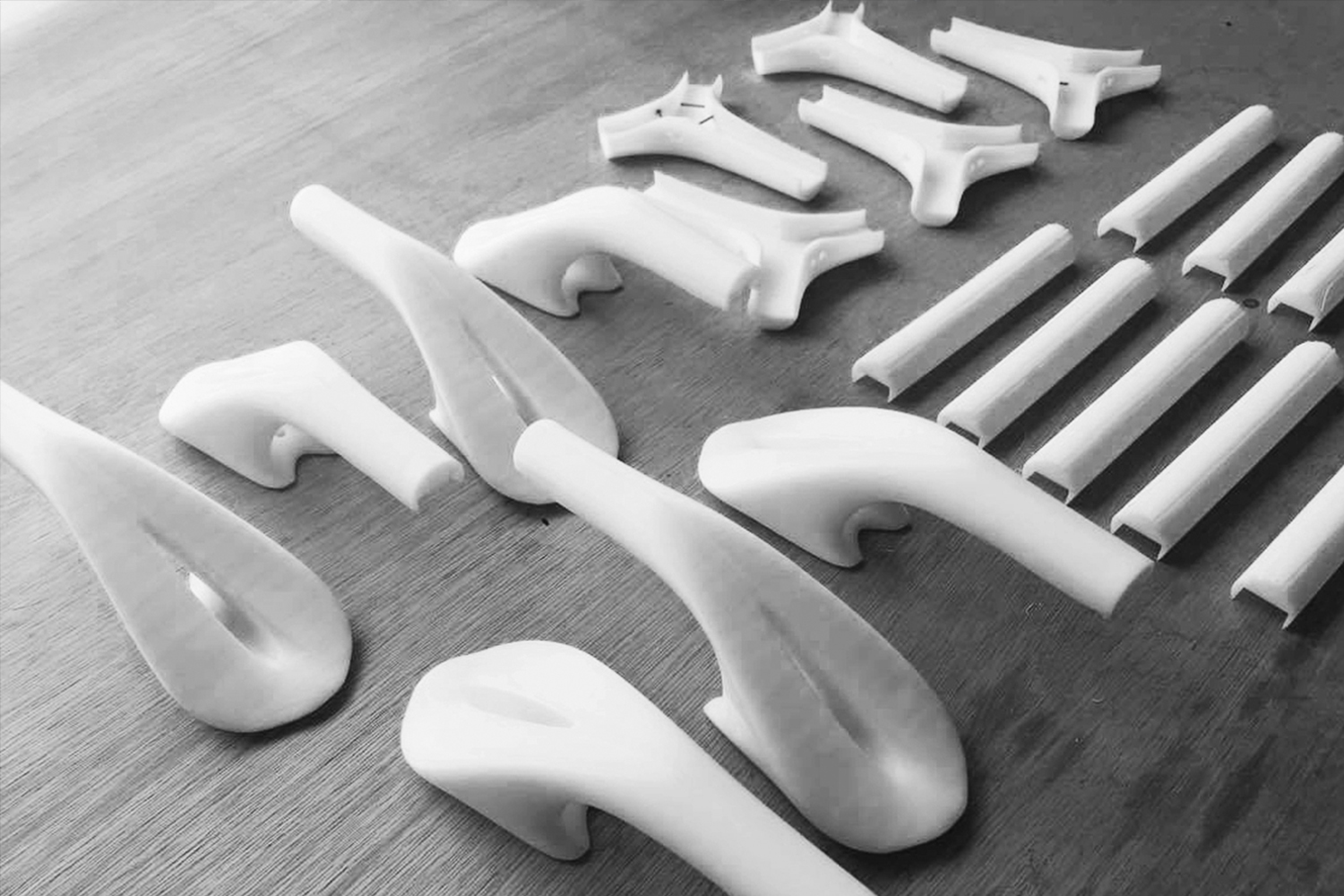
︎ 3D Printing Elements
4 ABS plastic units can be assembled more than 10 results.

︎Build the Lighting System
Integrating screws, fixed components, aluminum extrusions, wires into limited space of 3D printed parts.

︎ The Combination of Additive and Subtractive Methodologies
Testing the lighting system of the Hexapod design on CNC milled Valchromat colored MDF.

︎ 2017 Taiwan Design Expro
Demonstrating the design prototype in “ Taiwan Design Expro: Bewin Ocean” exhibition.
# 04
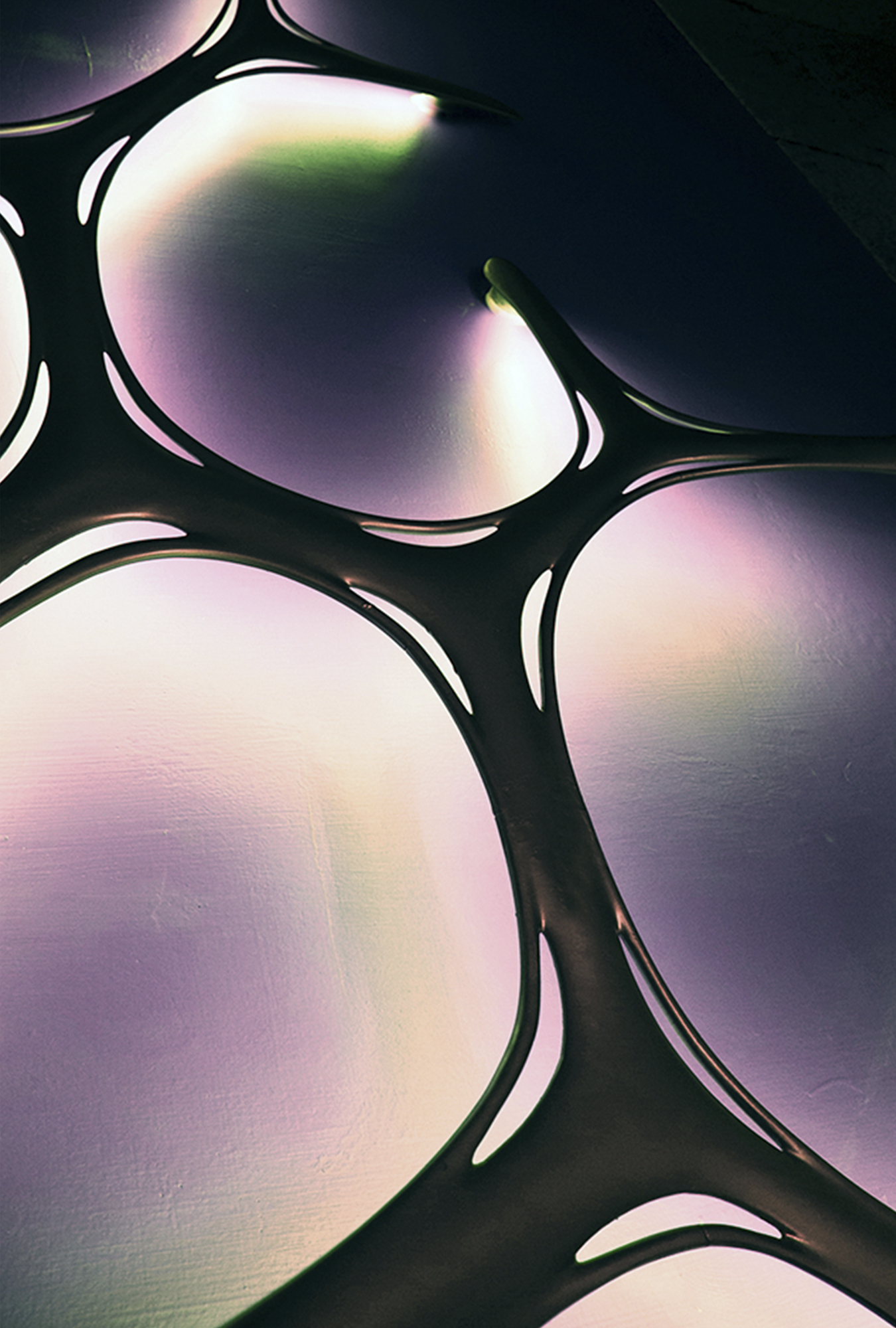
︎
Dekapede
Project Designer
( 2016. Spring-Summer)
Dekapede is a computationally defined wall lighting element derived from subdivided mesh geometry and 3D printed with Modex ABS 3D printing filaments demonstrating its direct to fabrication potential. The installation is the product of the “re-Inspired Contraptions” workshop series hosted by sKY_Associative in collaboration with Chimei | Modex. This special workshop event seeks to alleviate the existing barriers to this transformation in design culture, by lowering the cost of purchasing fabrication tools and sharing the necessary skills and knowledge to design with these tools in mind.
With support from the Wen Long Arts Foundation, 15 students were selected from the NCKU College of Design to participate in this three-part workshop where students built their own FDM 3D printers, learn to operate and maintain them, gain technical skills in 3D modelling and parametric design tools, and be exposed to industry professionals from the fields of design and art.

︎ 3D Printing Elements
The limited size printing parts were printed out by the 3D printers developed from "re-Inspired Contraption".
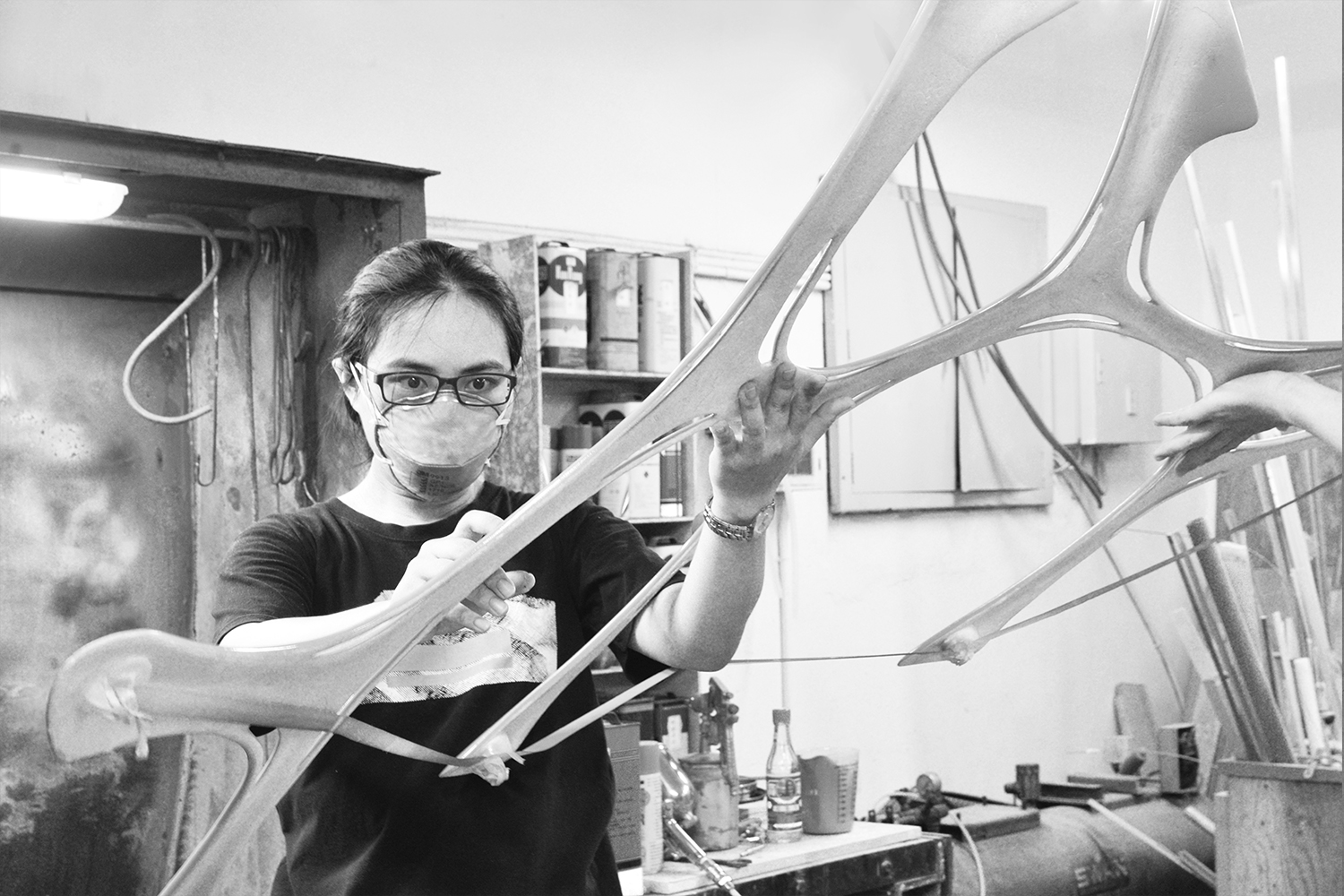
︎ Post-Processing
Gluing each 3D printing parts together and then sanding the surface after printing the primer.
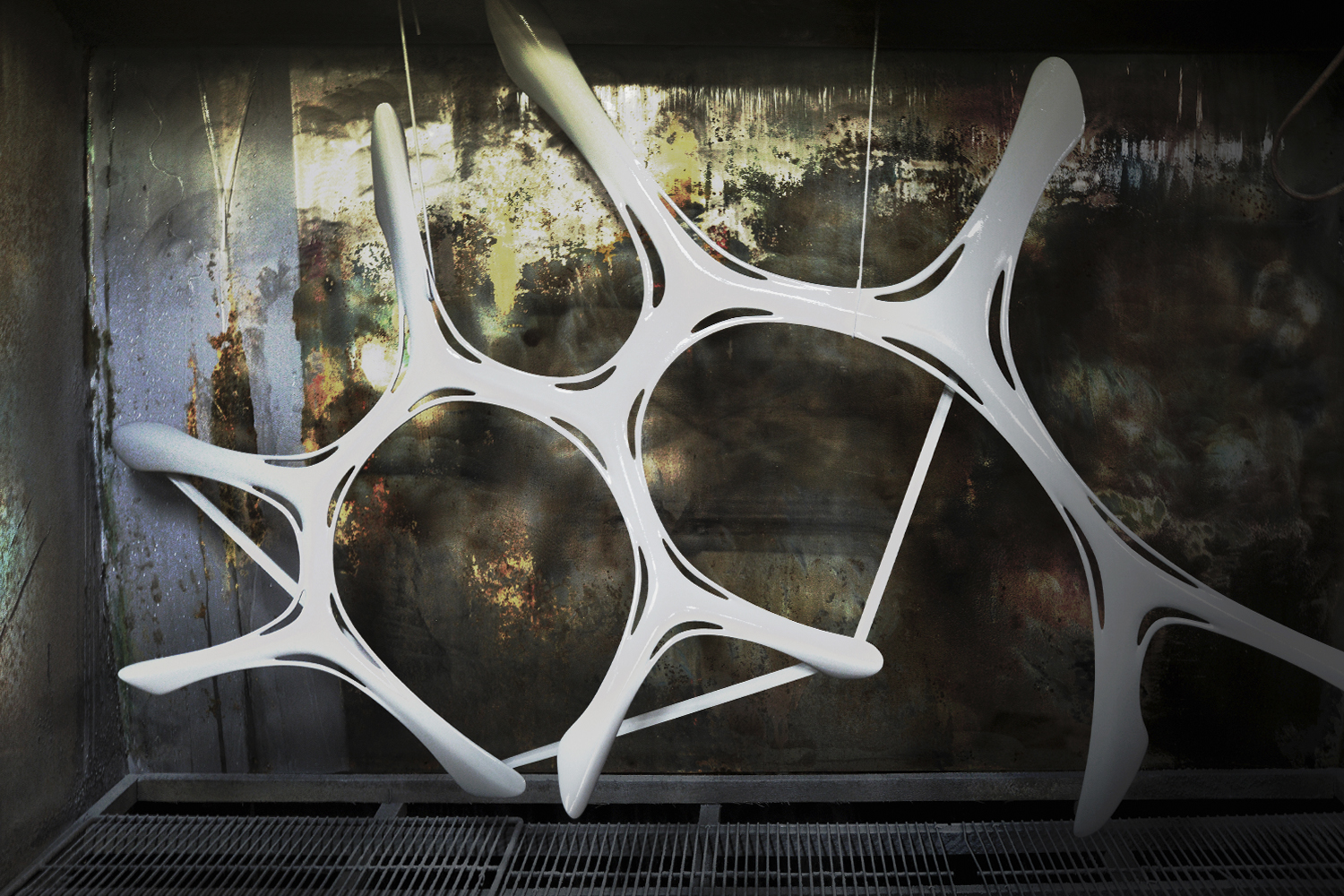
︎ Spraying Primer and Chromatic Paints
*

︎ Dekapede hangs on the NCKU Chub@coffee entrance wall
*
# 05
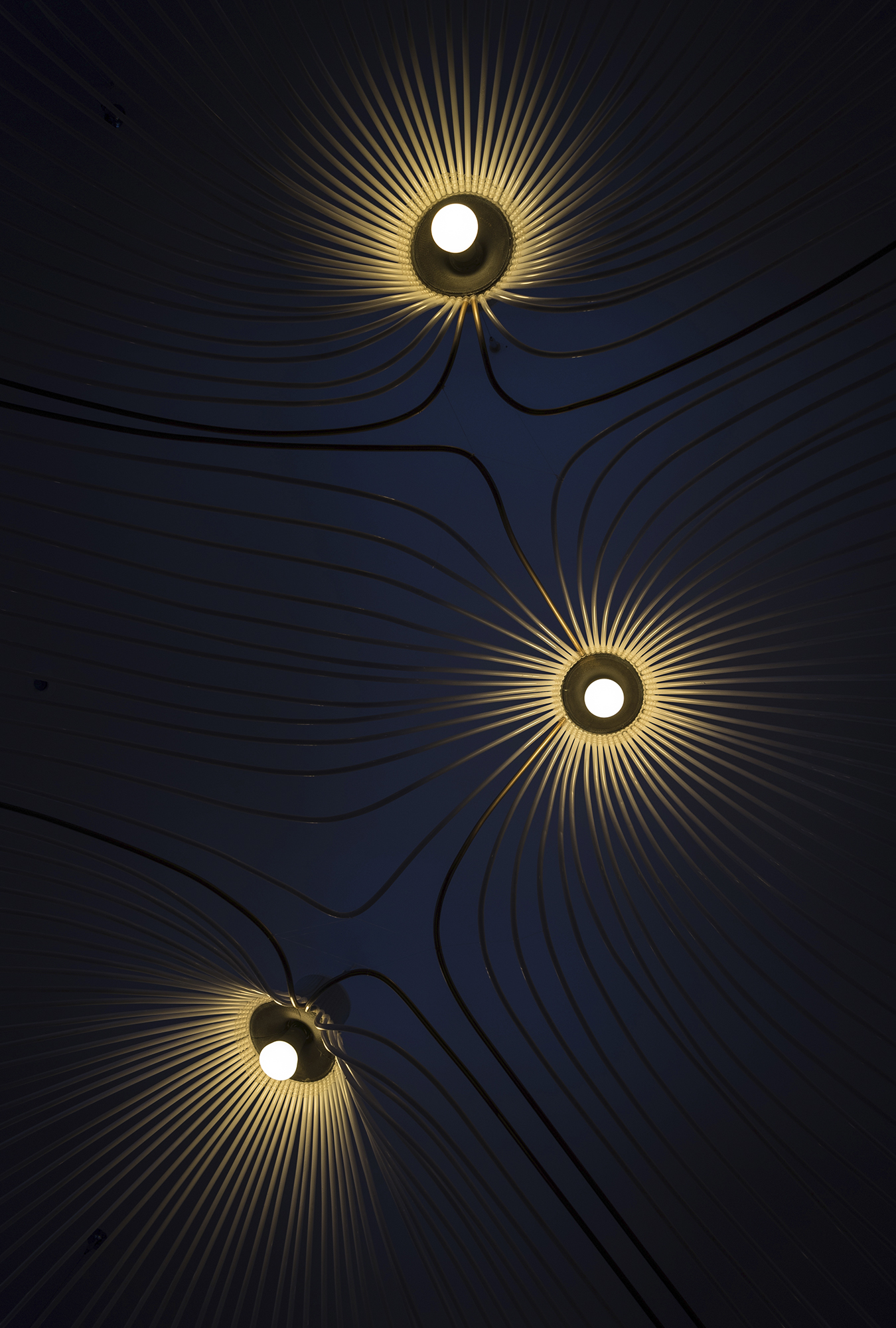
︎
Vector
Series
Lead Designer
( 2014. Summer-Fall )
The Vector Series, the bench and lamp installation, combines existing manufactured components and custom digitally fabricated elements by using math-based field vector algorithms. The relationship between the bench and lamp came about through the desire to reconsider the heat forming fabrication process of the lamp, and play off the idea of reuse and re-appropriation. Moreover, the lamp utilizes interactive lighting components developed by Philips to create a responsive environment that alters the ambiance of the installation space. The combination of existing manufactured components and custom digitally fabricated elements illustrates the significance of collaboration between industry and design.
As part of the Global Dialogue: Tainan x Dutch Design exhibition, the part and mold bring to mind thoughts of process, history, and memory, which are built into the parametric design tool in which the project was developed.

︎Insert Photoresistor
Installation of proximity sensors for interactive control of PHILIPS Hue light settings.
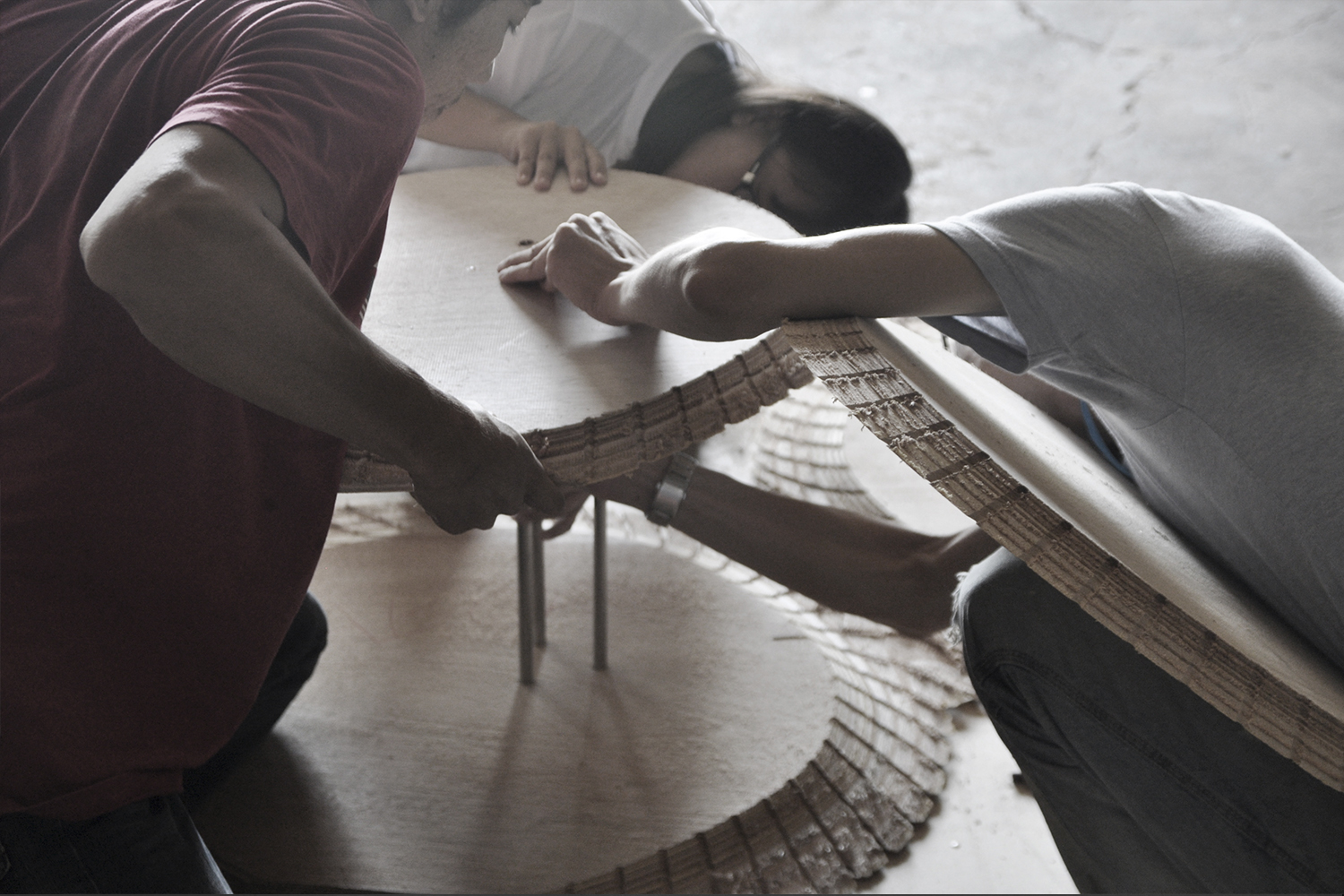
︎Assemble CNC Layer by Layer
Final assembly of the CNC plywood bench parts.

︎ Vector Lamp Fabrication Process
Forming acrylic tubes on the mold and testing the lighting system.
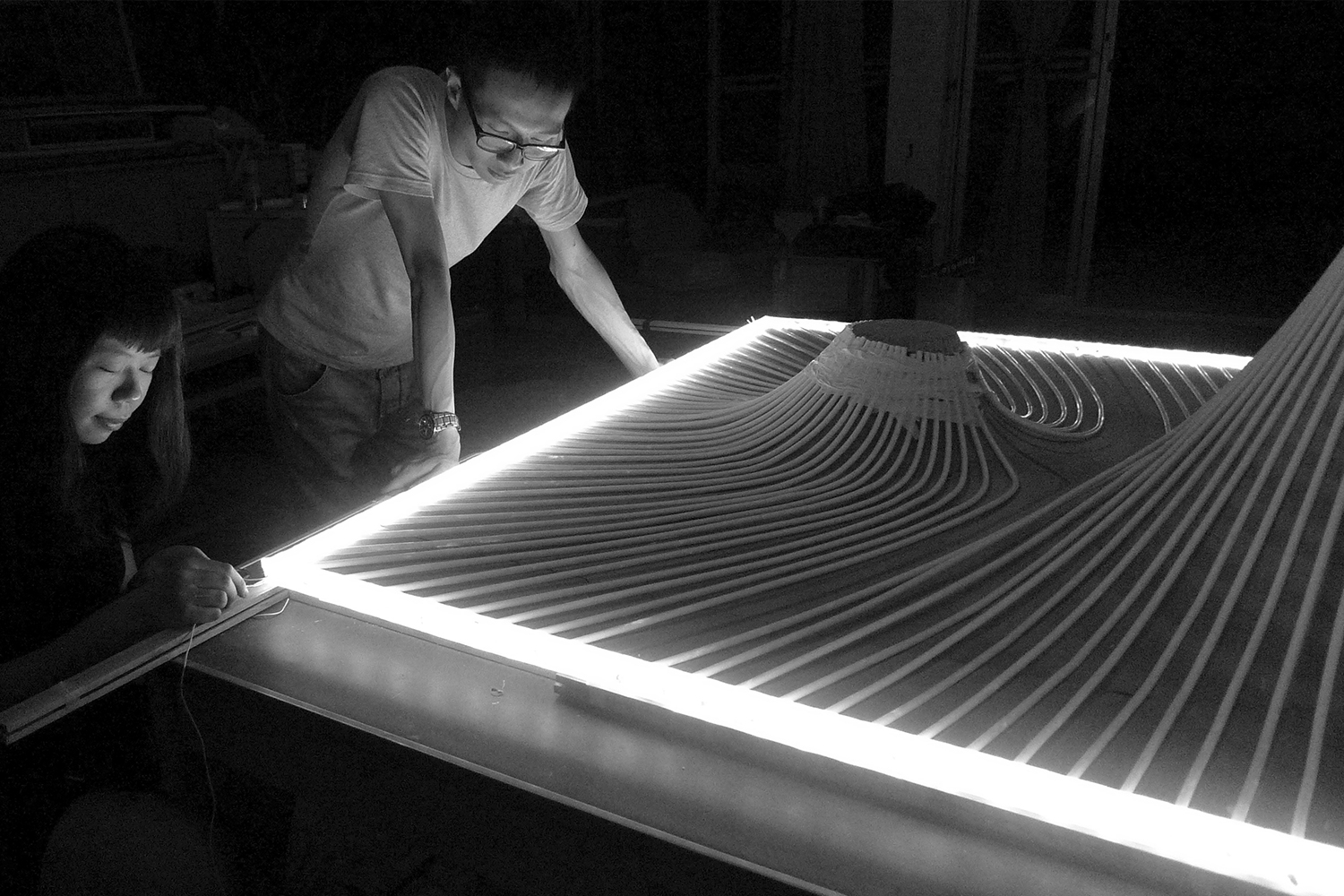
︎Testing Lighting Effect
*