# 01
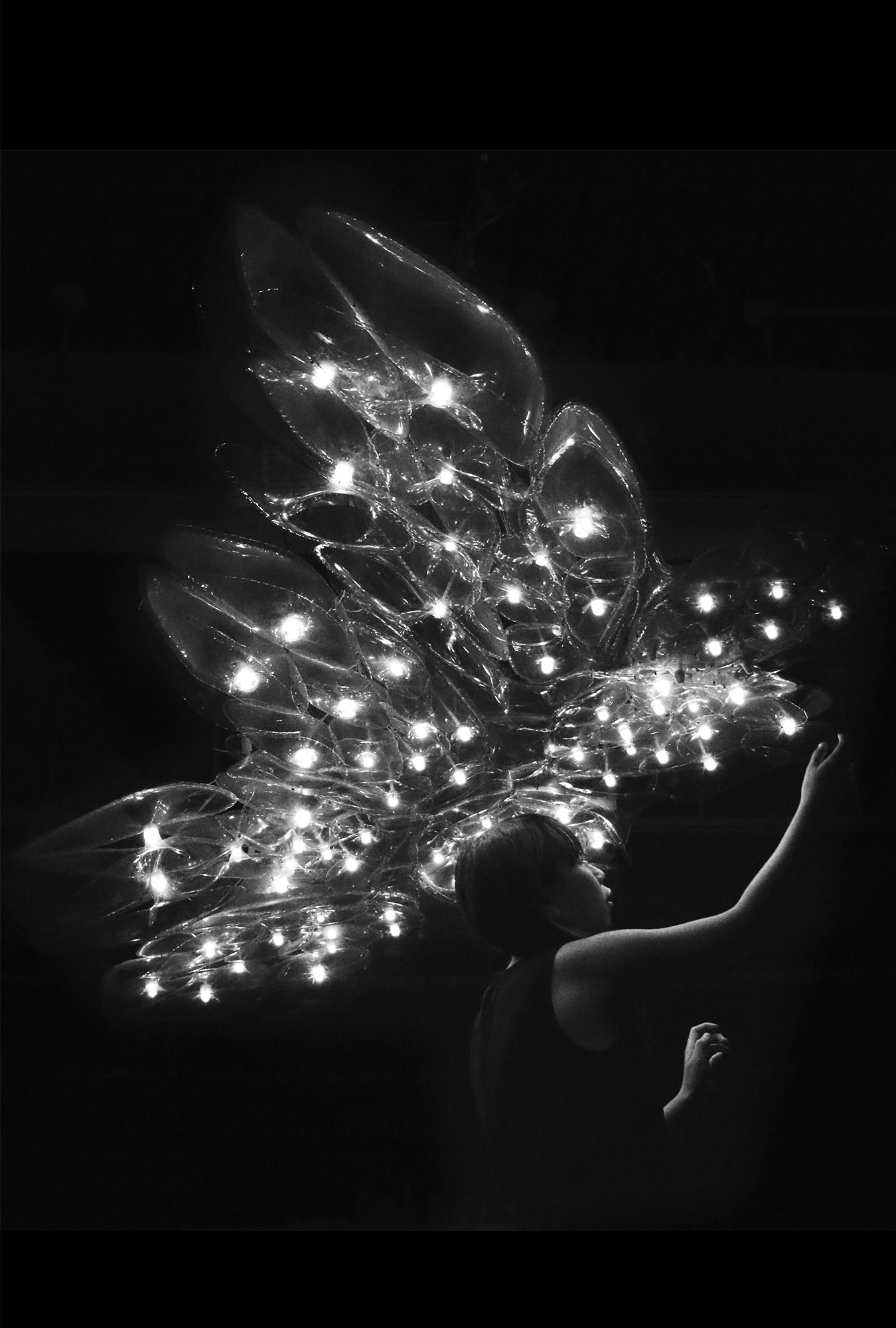
︎
Fasciner
Project Designer
+ Researcher
( 2016. Summer-Winter )
Fasciner, 2-meter x 1.5-meter x 0.3-meter large lamps, was composed of over 150 different units. The connection of each LED shading unit is accomplished through joints that have different heights, shapes, and sizes. The complexity of this joinery is required to facilitate the formation of such multi-directional curved surfaces. To address this issue, a device that can precisely control the fabrication process is required. The computationally controlled Variable Forming Machine was thus designed and built for this challenge.
Through the modification of traditional manufacturing machines to accommodate parametric control, the Fasciner Lamp demonstrates how the dialogue between designers and machine can allow us to revisit a craftsman-like mode of making.
as a part of Master thesis project "Plastic Formation: Exploring Material System in Digital Fabrication"; shortlisted Industrial Design Award INDUSTART.
The Variable Molding Machine: Fasciner

︎ Variable Geometry Forming
Producing 208 different units through Variable Forming Machine.

︎Post Processing
208 different units were assembled together by rivets.

︎ LED Light Installation
Using Arduino UNO broad to develop lighting effects with sensors.

︎ Lighting Control Tests
Using Arduino UNO broad to develop lighting effects with sensors.

︎ LED Light Installation
Using Arduino UNO broad to develop lighting effects with sensors.
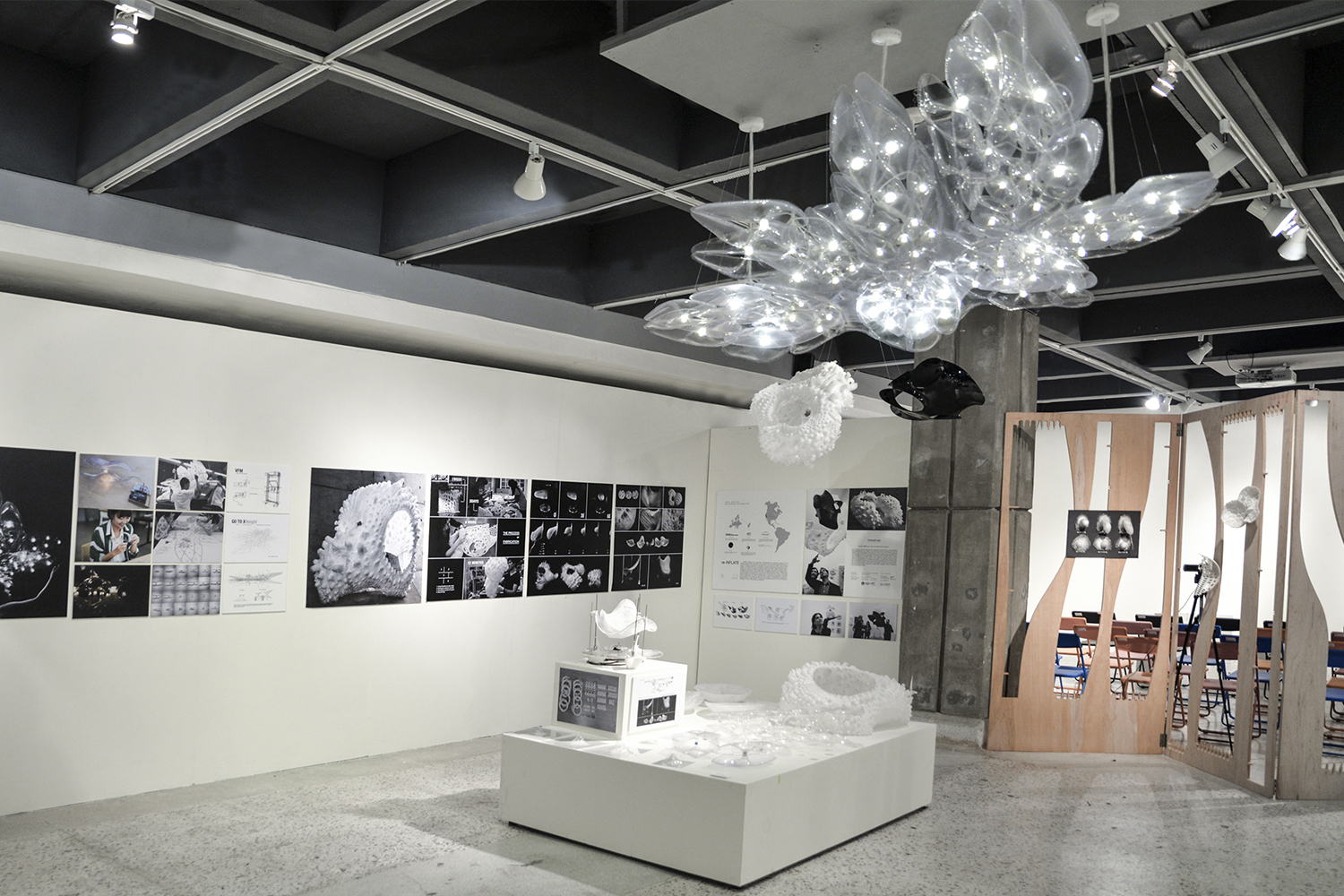
︎ Exhibited at NCKU art center
Displaying this project at "re-INSPIRED CONTRAPTION" exhibition, Jan. 7-18, 2017.
# 02
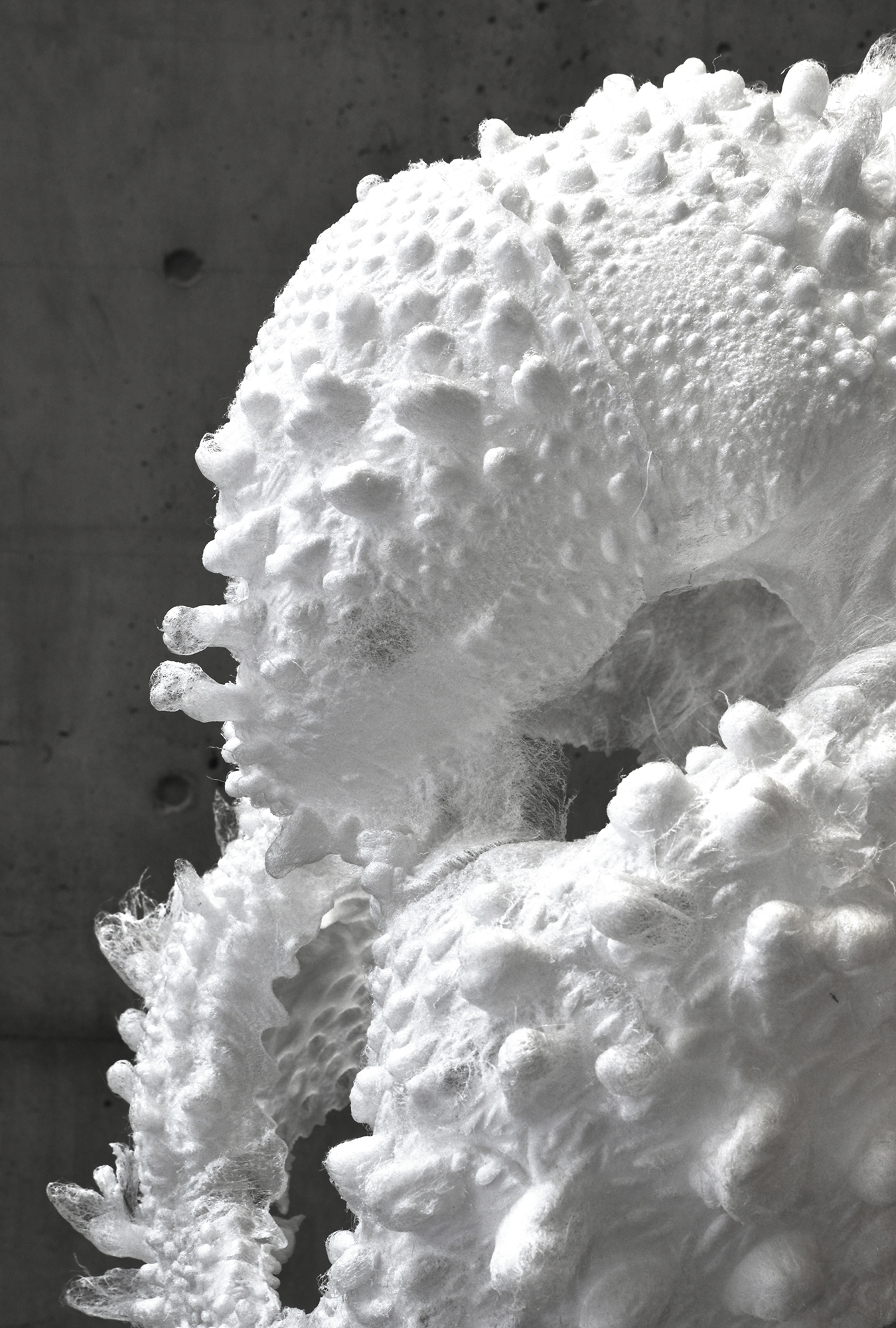
︎
re-Inflate
Project Designer
+ Researcher
( 2015. Spring-Fall )
In re-Inflate , I investigated the translation and transformation of digitally captured data to design form and the emergent characteristics of the spray forming fabrication process. In the spray forming process, a specially designed spray head is used to deposit semi-liquid polypropylene fibers onto the various molds. The final sprayed 3D printing part inherits not only the form and shape of the original mold but characteristics of the sprayed material fabrication process such as its translucent textile/fiber-like quality and the swollen blisters which become essential elements of the final design.
Through this experimentation and research, this project is informed by this process on multiple scales of application from interior building finish to overall formal expression.
shortlisted in international wearable competition RESHAPE 15 and Idustrial Design Award INDUSTART.
The new approach of spray forming process: re-INFLATE
